The electroplating barrels are intended for coating of small parts in bulk. This type of treatment enables to reduce much the complexity due to the mounting/demounting of parts, which decreases the overall production costs. The coating in the rotating barrel ensures the uniform coating. The polypropylene barrels are used for the majority of processes, and the temperature of the working solutions may reach +80 °C. For some chemical coatings, the stainless steel barrels, characterized by high abrasion resistance, are used.
First patent No. 2122606 for "Barrel for electroplating of parts" was obtained in 1994.
First patent No. 2122606 for "Barrel for electroplating of parts" was obtained in 1994.
Design of the electroplating barrels
The electroplating barrel, manufactured by Poliplast, is made, as a rule, in the form of a hexagonal prism. At the end faces, the barrel has gears intended to put the barrel in motion. The faces of the prism are fastened to the gears with strong ties, made of polypropylene or titanium, depending on the length of the barrel. On one of the faces there are removable lids, through which the treated parts are loaded/ unloaded. The barrel's sections have perforation holes and an embossed inner surface, which prevents flat parts from sticking on them. In some models, the internal space is divided into sections with a partition. The size of the perforation holes is 1x1 mm or 2.8x2.8 mm.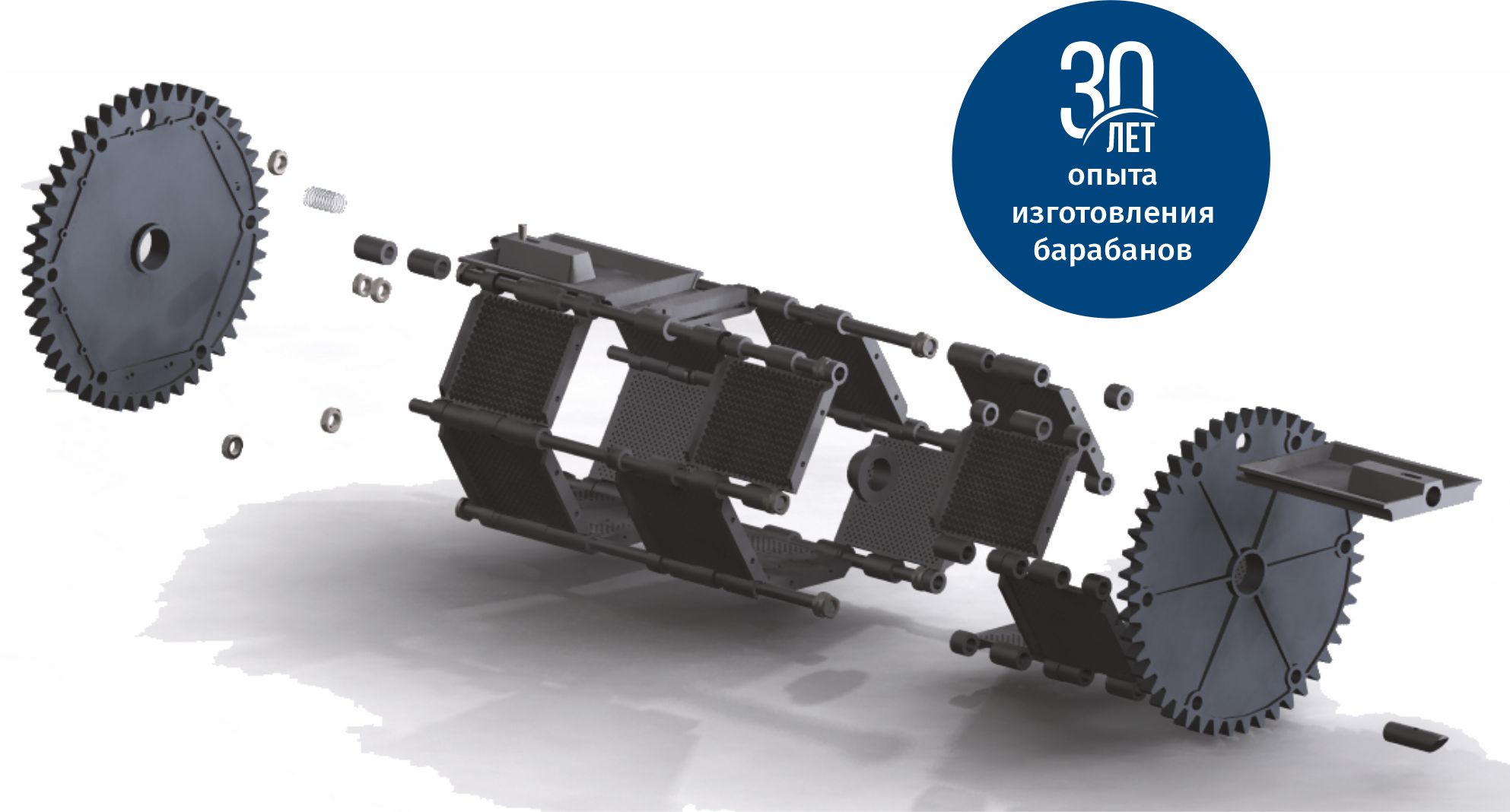